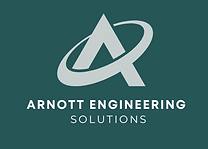
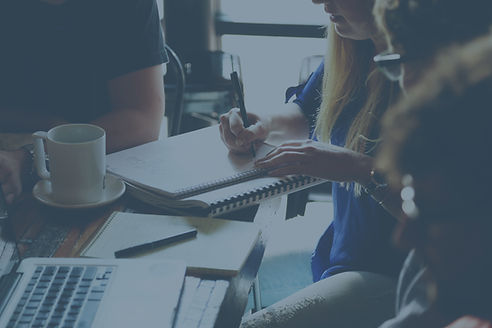
![1[1].png](https://static.wixstatic.com/media/e971e4_e6222a01c4244af499e842abddadc15f~mv2.png/v1/crop/x_0,y_174,w_3847,h_3108/fill/w_95,h_77,al_c,q_85,usm_0.66_1.00_0.01,enc_avif,quality_auto/1%5B1%5D.png)
Experienced engineering consultant specialising in materials, process engineering, new product development, and continuous improvement. Expert in optimising manufacturing processes, managing CAPEX projects, ensuring quality compliance, and driving cost reduction and automation. Skilled in process validation, quality management and subcontractor relations.
"35 years of experience"
.png)
C areer Milestones at Orchid Orthopaedics
​
Development Manager (2010):​​
​
-
Working closely with the quality group, focusing on critical scrap reduction and validation projects. Drove advancements in special processes, quickly earning a promotion to a Senior Management position within six months.
​
Engineering Manager – Hot Metals​
​
- Directed ISO13485 compliance for special processes, including validation conformance—a pivotal project as no prior special process validations existed at the time.
-
Led rigorous training for myself and my team, ensuring top-tier validation expertise and consistent quality standards.​
-
Reduced scrap rates from 10% to 4% within 12 months, achieving annual savings of approximately £350,000 across casting and forging value streams.
-
Managed the Process Engineering Team and Test Laboratory, supporting hot metals and production testing for all implant products.
​​
Head of Engineering (promotion after 18 months):
-
Oversaw New Product Introduction (NPI), process engineering, and test labs across all casting, forging, and machining value streams, managing a team of over 20 engineers​
-
​This position played a crucial role in driving business growth and fostering technical innovation across the Orchid facility. By implementing new processes and technologies, it helped enhance operational efficiency and competitiveness, ultimately contributing to the overall success of the organisation.​​​
​​
Technical Manager – Hot Metals Division:​​
​
-
Transitioned to a specialized, global role with a technical focus, supporting new equipment integration, process improvement, and collaborative initiatives across Orchid's international facilities.
-
Advanced additive manufacturing processes, supporting the development of large-scale implant production using additive techniques—an innovation that transformed implant manufacturing.
-
Head automation of engineering and NDT (Non-Destructive Testing) processes across the site, resulting in enhanced productivity and significant cost savings.
-
Conducted significant work on material efficiency and formulation innovations, driving forward complex material engineering and scientific advancements.
-
​
Career Highlights at DePuy, Johnson & Johnson
​
Laboratory Technician Apprentice (1987):
​
-
Began in R&D, focusing on the testing of raw materials and implant products, gaining foundational skills in material science and product testing.
​
Assistant Test Engineer (1991):​​​
​
-
Completed Casting School and took responsibility for developing and testing cast implant products, while gaining expertise in Non-Destructive Testing (NDT) methods, including Penetrant Inspection and X-ray. I worked closely with Level III NDT specialists to achieve a comprehensive understanding of advanced NDT techniques
-
Investigated customer returns, ensuring high standards of product reliability and quality.
-
Advanced to complex metallurgical investigations and product testing for the development and of New Product.
-
Supporting the development and implementation of the Bone Ingrowth sinter process for implants with the Leeds Facility.
​
Test Engineer (Promotion in 1994):
​
-
​​Assumed full technical responsibility for production support and special process development, particularly the Porocoat Sinter (Bone Ingrowth Coating) process.
- Enhanced the quality and reliability of the Porocoat sinter process through in-depth testing and process optimisation.
​
​
Process Engineer (2000):​​
​
-
Completed Six Sigma Black Belt Training, which laid the groundwork for leading significant continuous improvement projects.
-
Moved into Process engineering, taking on the daily support of the Special Processes and Production Test Laboratory
​
Engineering Team Leader (Promoted within Six Months):
​
- Led a team responsible for new technology introduction and special process support, marking several industry-firsts in orthopedic implant manufacturing:
-
Pioneered the introduction of the Citrisurf Passivation process on a fully automated cleaning and passivation line.
-
Introduced a fully automated FPI (Fluorescent Penetrant Inspection) line.
-
Developed an automated reclamation process for Porocoat powder, saving approximately $1 million annually.
-
Launched an electrostatic spray process for the Porocoat process, achieving preventative cost savings of $2.5 million. This is project won the J&J sustainability award for the positive environment impact of the change.
-
Managed these projects as Six Sigma Black Belt initiatives, aligning with DePuy's continuous improvement goals.
​
Engineering Group Leader (Promoted in 2006):​​
​
-
Led substantial cross-site projects at J&J to optimise special processes, applying Six Sigma methodologies across all continuous improvement projects for heightened efficiency and reliability.
-
Conducted supplier audits and qualification processes across a substantial network of suppliers to meet stringent J&J standards.
-
Supported New Product Introduction (NPI) in collaboration with Supplier Quality and Purchasing Managers, ensuring quality and certification compliance for casting and forging suppliers to J&J facilities.
​​
​
​